Cone crushers are highly efficient crushing equipment widely used in ore processing and construction material production. Understanding their working principle and mastering maintenance tips can not only extend the equipment's service life but also ensure the stable operation of the production line. This article will detail their operation mechanism and key maintenance points.
Working Principle
The core of a cone crusher lies in the synergy between the moving cone and the fixed cone. During operation, the moving cone performs a swinging motion driven by the eccentric shaft, forming a continuously changing crushing chamber with the fixed cone. Materials entering the crushing chamber are subjected to multiple forces such as compression, shearing, and bending, ultimately being crushed to the desired particle size. This laminated crushing method is not only efficient but also effectively reduces equipment wear.
Maintenance Tips
To maintain the good performance of cone crushers, the following maintenance points are crucial:
- Lubrication Management: The lubrication system is key to equipment operation; regularly check the oil quality and replace the lubricating oil to avoid excessive wear of components due to insufficient lubrication.
- Wear Parts Inspection: Components like the crushing wall and mantle are wear parts and should be regularly checked for wear and replaced promptly when necessary to ensure crushing effectiveness.
- Hydraulic System Monitoring: The hydraulic system is responsible for adjusting the discharge opening and protecting the equipment; regularly check the oil pressure and temperature to ensure they are within the normal working range.
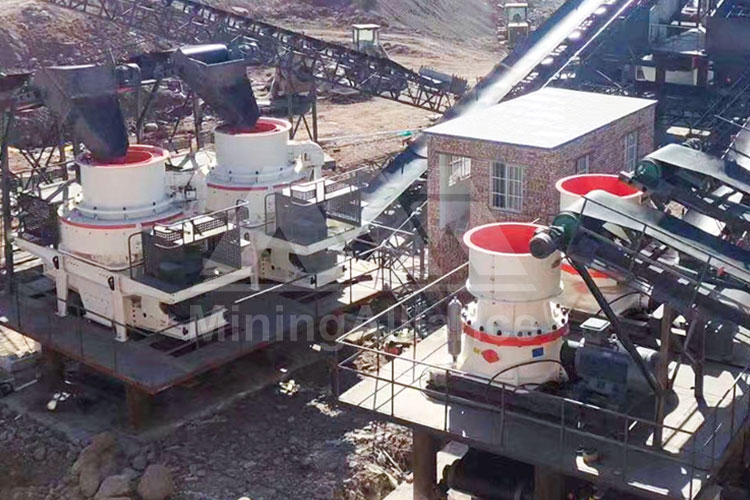
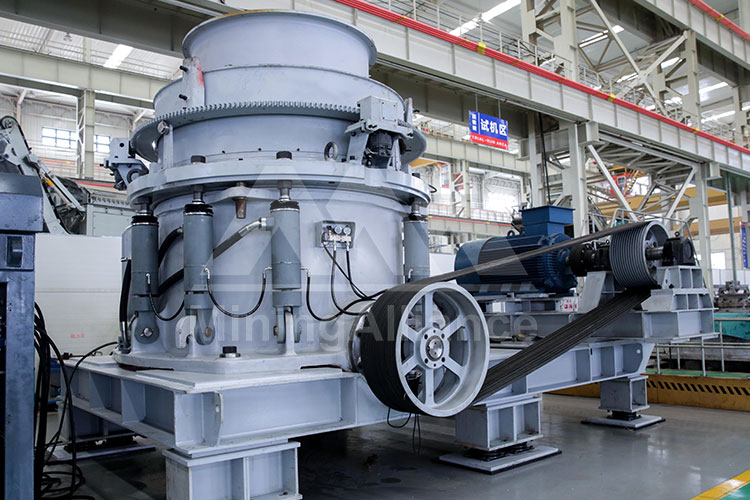
Technological Advancements
In recent years, cone crushers have made significant progress intechnology and design. New equipment uses high-wear-resistant materials for key components, greatly enhancing durability; meanwhile, the introduction of intelligent control systems makes operation more convenient and extends maintenance cycles. These innovations not only reduce operational costs for enterprises but also improve the reliability of the equipment in complex working conditions.
Optimization of Work Efficiency
To further enhance the work efficiency of cone crushers, technicians have adopted various optimization measures in design and operation. Firstly, through precise calculations and simulations, the shape and size of the crushing chamber are optimized to ensure even force distribution on materials during crushing, reducing ineffective energy consumption. Secondly, the equipment features an adjustable eccentric distance design, allowing operators to flexibly adjust the amplitude and frequency of the crusher according to material characteristics and production needs to achieve the best crushing effect. Additionally, modern cone crushers are equipped with automatic discharge systems that can quickly expel materials when the crushing chamber is blocked, avoiding equipment downtime and ensuring the continuous operation of the production line.
Common Failures and Troubleshooting
Despite the high reliability of cone crushers in design, some common failures may still occur during long-term operation. Understanding these failures and their troubleshooting methods can help reduce downtime and ensure stable equipment operation.
- Failure One: Abnormal Vibration
This may be caused by uneven wear of the moving or fixed cone liners or insecure foundation installation. The solution is to regularly check the wear of the liners, replace them in time, and ensure that the foundation bolts are tightened. - Failure Two: Unstable Hydraulic System Pressure
This could be due to contaminated hydraulic oil or oil pump failure. It is recommended to regularly replace the hydraulic oil and check the working condition of the oil pump and valves. - Failure Three: Discharge Opening Blockage
Often caused by high material moisture or oversized particles. This can be prevented by adjusting the feeding speed and using pre-screening equipment.
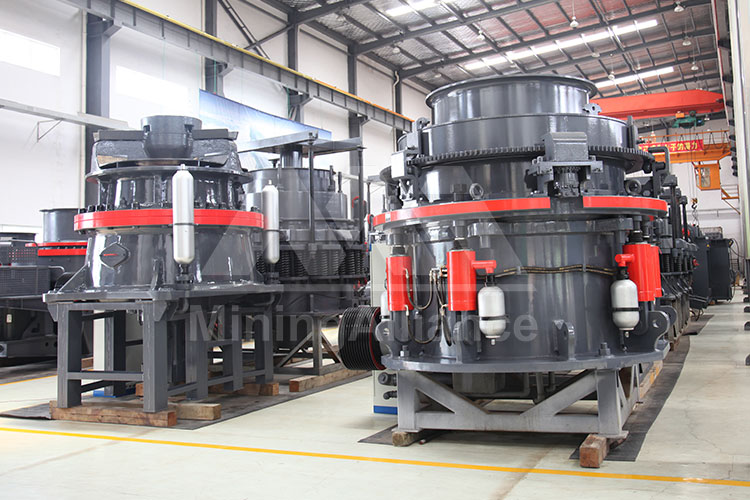
Importance of Operator Training
The maintenance and efficient operation of cone crushers rely on professional operators. Enterprises should regularly provide equipment operation and troubleshooting training to employees to ensure they are familiar with the equipment's operating principles and key maintenance steps. For example, understanding how to correctly adjust the hydraulic system or replace wear parts can effectively avoid equipment damage due to improper operation. Additionally, training can enhance employees' safety awareness, reducing potential risks in production.
Preventive Maintenance Strategies
In addition to routine maintenance, adopting preventive maintenance strategies can significantly extend the service life of cone crushers. For instance, by installing sensors to monitor parameters such as vibration, temperature, and oil pressure, potential issues can be detected early and addressed promptly. This data-driven maintenance approach not only improves equipment reliability but also optimizes maintenance plans, avoiding unnecessary repair costs. Especially in high-intensity mining environments, preventive maintenance has become an industry trend.